Factory Process
The processes used for in-factory construction of buildings and levels of automation vary among companies, but typically, the factory building process is organized like an assembly-line production. There are many time savings and other productivity gains compared to on-site construction, as well as environmental benefits. Nothing works better to experience this way of constructing buildings than a factory visit.
Productivity Gains
This chart describes the schedule and where the time savings in the factory building process come from. The process allows for the construction of the building in the factory and developing the site at the same time—which is where the greatest time savings are realized. In addition, as buildings and modules are constructed in the factory, there is less disruption at the site, which speeds up site restoration after the building is installed and completed. Material procurement for a factory build is all but complete before the modules are constructed, which also reduces delays. For full modular construction, many reports quote at least 50% less construction time. Even for panelized construction—using pre-constructed walls or floors, for example—construction time savings can be as much as 40%.
Other productivity gains that can be achieved in factory-built construction include increased production rate, less time spent for processing payments and invoicing, reduced time for on-site inspections and fewer vehicles used for site supervisors.
Design and permits (pre-construction)
The design process for factory-constructed buildings is the same as for site-constructed buildings, with the additional consideration of transportation requirements (allowable width, height and weight). Client specifications and building code requirements at the destination location are incorporated into designs in the same way they are for a site-built home or building, and permits are processed with the jurisdiction where the building will be located. For multi-unit projects, an assembly plan and project management plan typically detail the responsibilities of the local builder, the factory builder, and the installation and assembly crew.
During the pre-construction process, choices are made about building materials, appliances, products and interior and exterior finishing. These choices need to be finalized and confirmed before construction in the factory begins.
Step-by-step process
Factory processes and levels of automation vary among companies, but typically, the factory building process is organized like an assembly-line production. As the building or module is assembled, it moves along the line from one workstation to the next. It can be rolled, lifted by crane or pulled forward along the line. More time-consuming and specialized work such as the construction of trusses, doorframes, kitchen cabinets, or pipe sub-assemblies, for instance, are usually fabricated away from the assembly line. Wherever possible, the construction of the buildings is done at ergonomic heights for optimized working positions.
The production sequence typically follows this order:
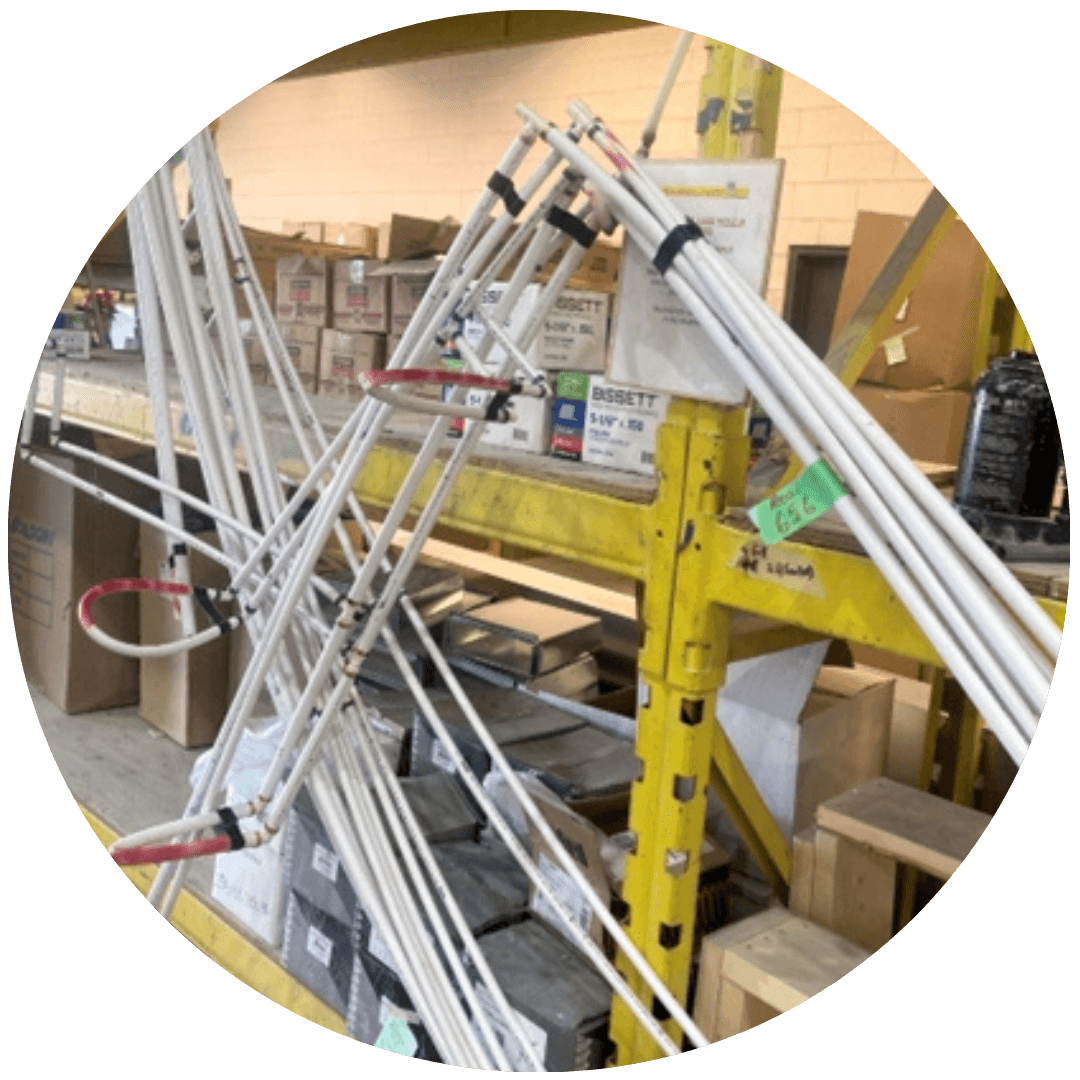
Inside-out construction in a temperature-controlled environment
One of the tremendous advantages of factory-built construction is that each module is built “from the inside out”, which provides for straightforward and effective installation of insulation—no gaps in corners, behind electrical outlets or other hard-to-reach areas. This makes for very airtight and energy-efficient buildings, and for homeowners, this means no cold spots or drafts, and greater indoor comfort.
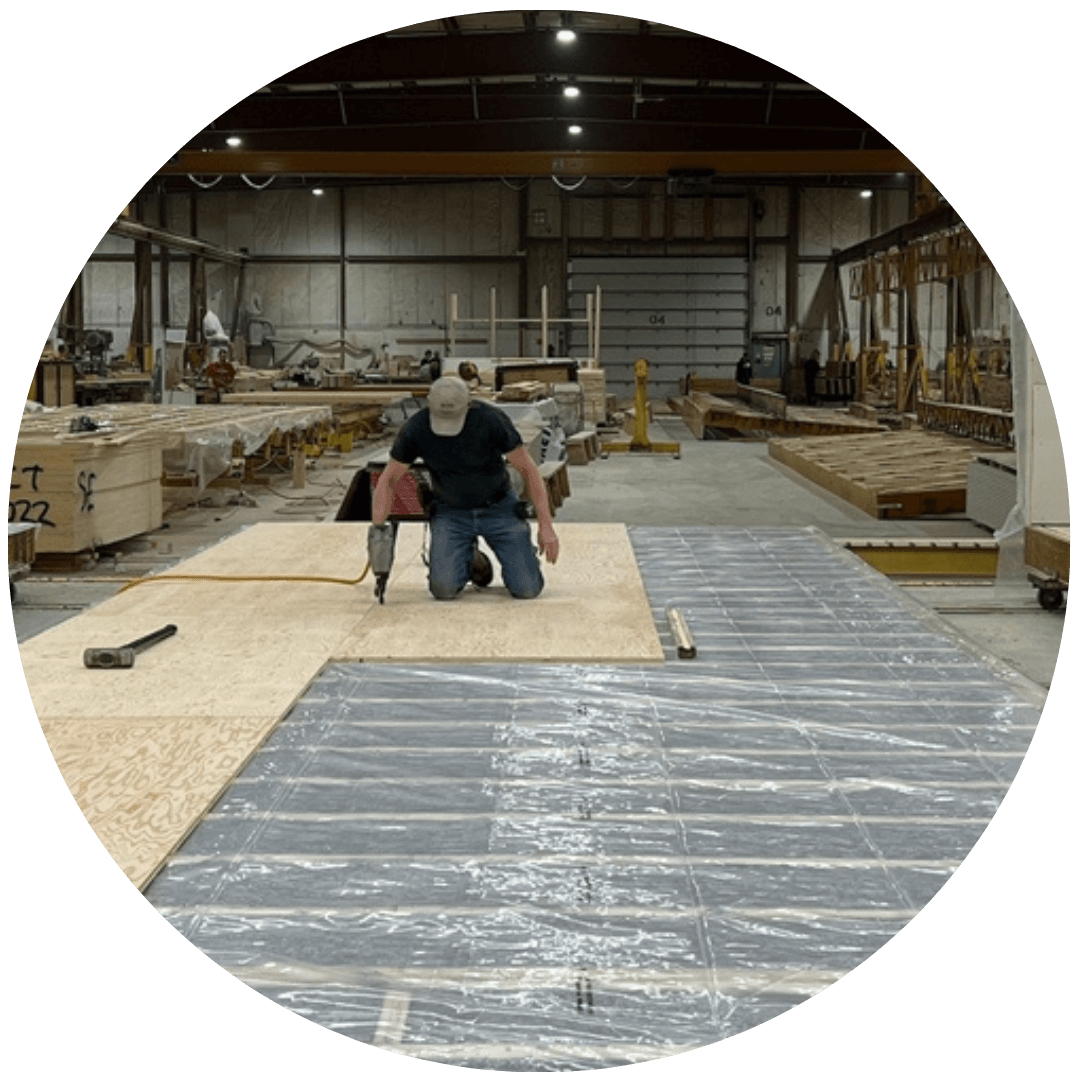
Transport to the site
Once the exterior siding and roofing are installed, the buildings, modules or sections for a given project are moved outside to prepare them for transport. This step is called staging. Modules and sections are then transported by road, rail, barge or air to their final destination.
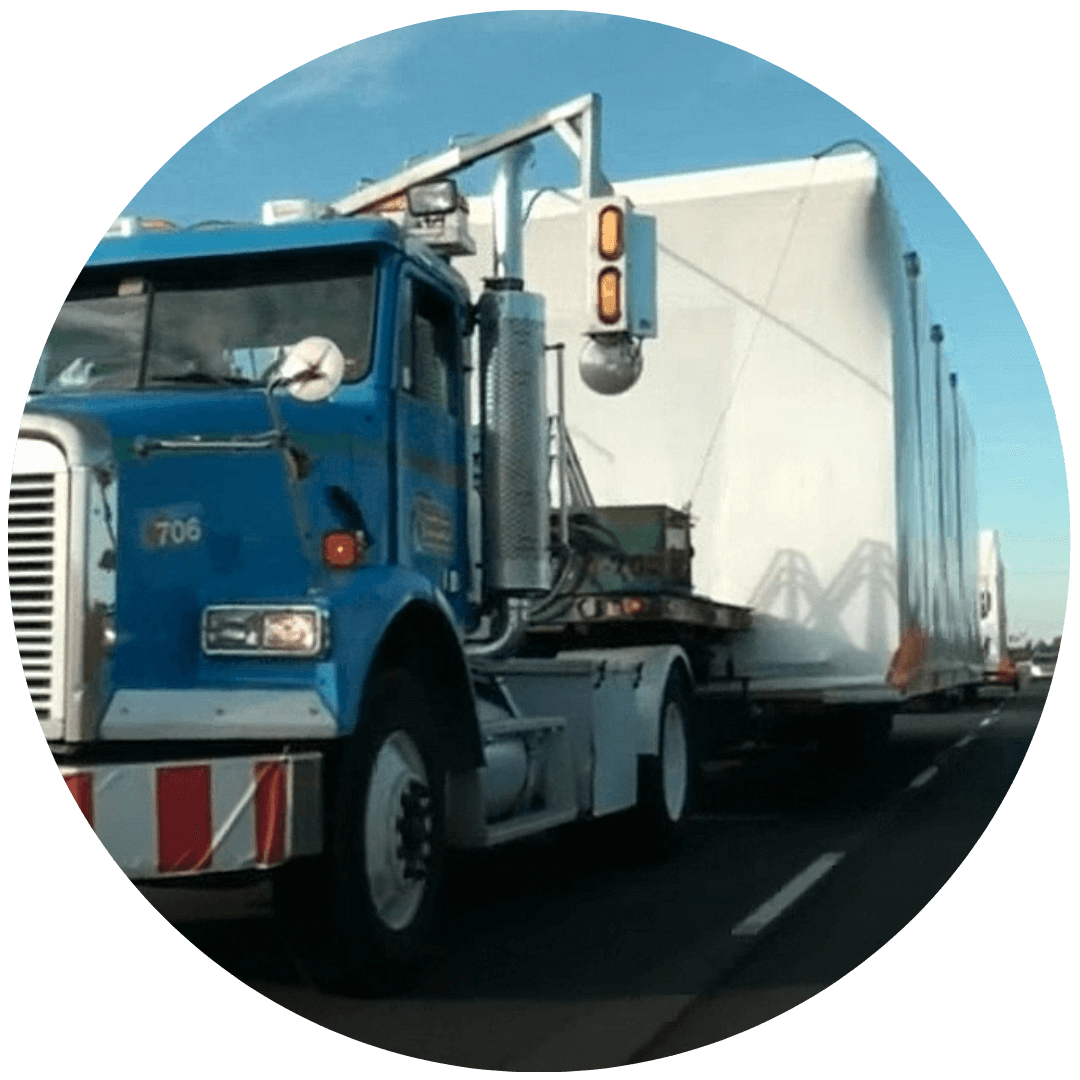
Set-up and finishing
Once on the site, the home is placed on its foundation, electrical and plumbing connections are made, and finishing is completed. In the case of a multi-module or multi-unit building, modules are placed as the plans and the numbers on the modules dictate. Modules are matched and set onto the sill plates or on top of each other. This is a very precise process as the module is held by the crane and adjusted manually until the bottom plate of the wall that joins the two sections sits exactly on the sill plate or the unit below. Once the modules and sections are firmly assembled to make a building, the joints are covered with siding and the site is restored. The resulting houses and buildings are indistinguishable from site-built projects.
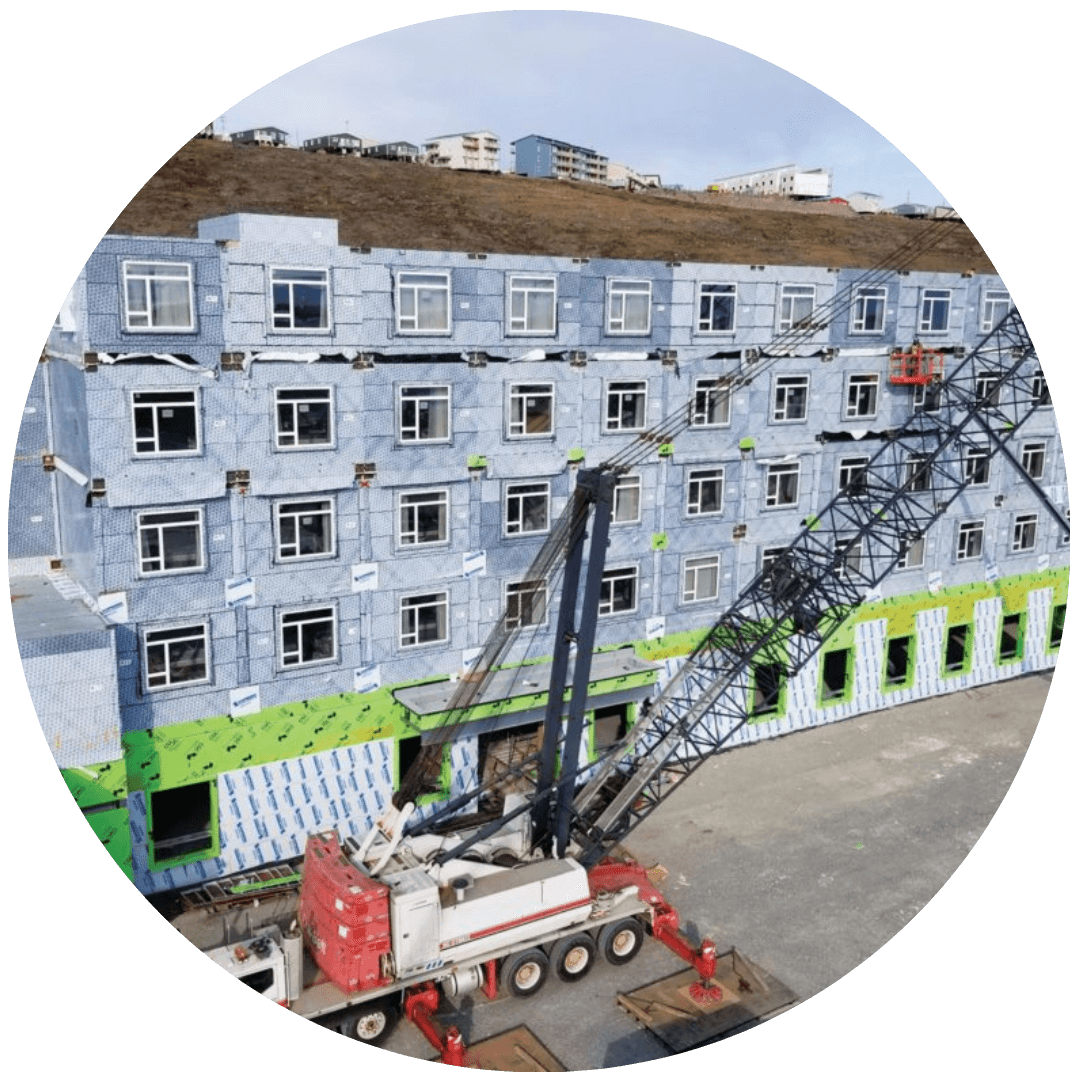
CHBA's "Working with Modular" Webinar Series
“Working with Modular” is a six-part webinar series highlighting the features and benefits of modular construction. The content is designed to inform on-site builders and developers, code officials, municipal planners and housing specialists, government departments, lenders, warranty providers and other stakeholders engaged in the residential construction industry. We would like to acknowledge the support of the Canada Mortgage and Housing Corporation in the development of the webinar series as well as Altus Group for their work in the project.
To watch the videos in full-screen mode, click on the YouTube icon in the bottom right of the video after you hit play.
The Factory-Built Process
(December 15, 2022)
This webinar describes how a modular building is constructed in a factory, transported, and set up and finished at the site, discussing potential impacts on costs and productivity.